[ad_1]
Maintenance, Repair, and Operations (MROs) play a significant role in the operational well-being of every manufacturing facility or plant. Simply put, the better the MROs are, the longer a manufacturing facility runs without hiccups. However, when the MROs are inadequate, a manufacturing facility is likely to encounter several challenges such as budget issues, operational challenges, and machine failure.
In this post, we’ll take you through the biggest challenges that manufacturing facilities face, along with solutions that are meant to overcome them. So, let’s get started.
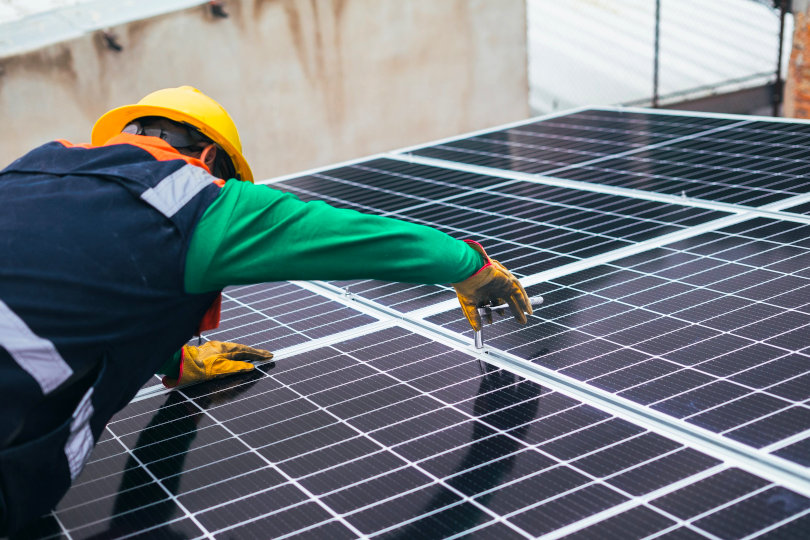
1. Unplanned Downtime
All machines are bound to run into technical issues sooner or later, and when they fail, they disrupt the operations of a manufacturing plant. On average, unplanned downtime of 800 hours is a problem that all manufacturing facilities experience each year. Even when a single machine fails, the productivity of an entire plant is affected.
All the processes that require the machines to be functioning properly are stalled as a result, and in such a scenario, bottlenecks are inevitable. If a manufacturing facility fails to anticipate unplanned downtimes, it can create problems in the entire supply chain.
The solution to this problem lies in having access to data that offers insights into the various parameters of machine operations. This allows manufacturing plants or facilities to carry out predictive maintenance, which is all about anticipating when machines will fail well before they actually do.
Putting this into practice would mean that the necessary repairs are carried out well before the technical problems serious enough to trigger complete machine breakdowns.
2. Variability in Maintenance Standards
Every manufacturing plant needs to have consistent maintenance standards that all maintenance personnel have to adhere to. Without proper communication of consistent maintenance standards, it is likely that personnel will resort to different methods every time the machines need to undergo maintenance. This is likely to result in problems, which end up being time-consuming to rectify.
Simply put, there shouldn’t be any ambiguity when it comes to establishing standard maintenance procedures and protocol.
That’s where the development of standard operating procedures or SOPs comes into the picture. Through the development of SOPs, maintenance personnel will be on the same wavelength in terms of what the maintenance work is, when it needs to be undertaken, and how it has to be executed. By codifying procedures, SOPs make it easy for maintenance personnel across all levels to follow instructions.
Having a central repository that allows all personnel to access SOP-related information efficiently is crucial.
3. Management of Maintenance Team
Managing maintenance personnel in a manufacturing facility environment is extremely challenging. However, without it, miscommunication is likely. Ultimately, when instructions aren’t communicated to all personnel clearly, it results in ambiguity and vagueness. As a result, plant operations are severely jeopardized.
The key to successful management of various maintenance teams lies in the use of digital tools for relaying instructions in an even manner to all.
For example, a central repository such as CMMS allows various employees and teams of a manufacturing facility to have even access to information. From handling predictive maintenance to management of checklists to automation of maintenance – CMMS manages both plant maintenance activities and teams.
4. Limited Maintenance Budgets
You need to remember that the budget set by a business as its maintenance budget depends on how profitable the business deems it to be. This can create a conflict between what the maintenance needs of a plant are and what is actually available based on the money set aside for maintenance purposes.
Differing opinions between business managers and maintenance managers may also come into the picture and affect the maintenance budget. These conflicts are all a result of the goals pursued by the business and maintenance teams, which are likely to be different.
The only way of sorting out this problem lies in striking a balance between the goals of the different teams and what is needed on the ground to make those goals achievable. For example, maintenance managers can discuss the cons of a limited maintenance budget with business management. Once the business management team understands that low maintenance budgets will sooner or later have an impact on profitability, the budgets will most likely be increased.
Most of the solutions to the challenges mentioned here lie in effective and efficient communication. As long as different teams respect and understand each others’ goals, solutions will always be only a few steps away.
[ad_2]
Source link