[ad_1]
Relativistic Space Launch from Long Beach, California is preparing to launch its first 3D-printed low-Earth orbit rocket.
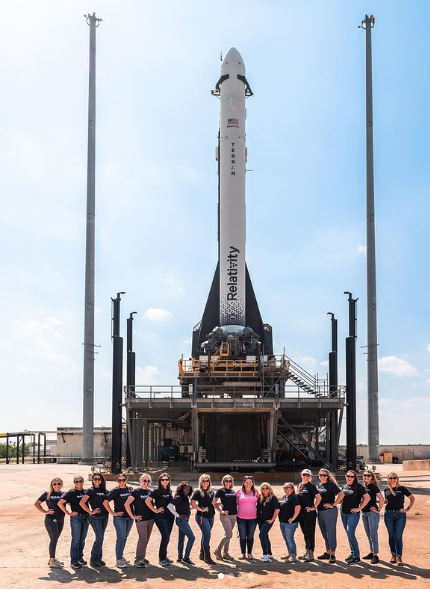
Image credit: Relative Position
The company, which is operating a 1 million square foot former Boeing facility of the future called ‘The Wormhole’, says its new additive manufacturing technique is cheaper and faster than conventional rocket manufacturing techniques.
Terrain 1 will use nine Aeon engines for launch and can theoretically carry a commercial payload of around 2800 pounds. (1250 kg) into low earth orbit. The engines use liquid oxygen and liquefied natural gas, which are precursors to fuel and suitable for reuse in rockets.
As with each phase of the rocket’s structure, Relativity will 3D print engine components for Terrain 1, making it the largest 3D printed object to test low-orbit flight, with 85% of the vehicle’s total weight 3D printed.1 The company plans to increase this figure to around 95% with 3D-printed weight in future iterations of its space vehicles.1
The world’s largest metal 3D printers
A relatively new 3D printing method could revolutionize the future of space travel and additive manufacturing techniques in general.
Earlier, the company confirmed that it was an additive manufacturing technology, as its largest metal 3D printers could only produce parts of around one cubic foot in total volume. Some parts of Terran 1 were 20 feet long, and the company had to practically reinvent the technology to produce a rocket capable of spaceflight.
In its proprietary manufacturing facility, Relativity began printing Terran 1 parts and prototypes using traditional vertical additive manufacturing techniques. However, Relativity has since adjusted its tactics and now uses the largest metal 3D printers in the world to print the Stargate horizontally at 7x speed.
The company has developed its own aluminum alloy to facilitate production, which does not require any fixed equipment.
The change from vertical to horizontal printing meant that the company had to adjust the physics of the print head, which facilitated faster print speeds. The team also uses machine learning techniques to ensure that errors are fixed in real time, making sure their method is smart – StartGate printers get smarter with every print run.
Relativistic, which says the team only takes about 60 days to produce rockets, looks set to overtake other commercial space companies and gain a foothold in the global economy, estimated to be worth around $350 billion.
Good luck, have fun
Initially for 8Th The launch, dubbed March, Good Luck, Have Fun (GLHF), has since been rescheduled and will resume on Saturday 11.Th March, from Cape Canaveral, Florida.
If successful, the company will move on to the next phase of manufacturing Terran, the first fully reusable 3D-printed rocket capable of carrying commercial payloads of up to 44,000 pounds. (20,000 kg)
With large-scale metal 3D printers front and center at Relativity Enterprise, the company is shaking up the commercial space industry by showing others that viable rockets can be created using alternative manufacturing methods and fewer components.
Conventional rocket manufacturing techniques require hundreds of thousands of parts, often hand-made and assembled, meaning years of design iteration and production before a rocket reaches the launch pad.
With this in mind and jointly developing the factory and rockets of the future, it strives to continue the development of innovative additive manufacturing techniques focusing on design, production speed and quality, 3D-printed rockets of future space travel.
Join the Relativity live stream here to watch Terran 1’s launch on Saturday, March 11, 2023, 10 AM EST.
References and further reading
- relative position (2023) relative position. Available at https://www.relativityspace.com/
[ad_2]
Source link